Introduction
The manufacturing industry is undergoing a monumental transformation, largely driven by advancements in artificial intelligence (AI). As manufacturers face increasing pressure to boost productivity, reduce operational costs, and maintain high-quality standards, AI has emerged as a game-changer in revolutionizing production line automation. The integration of AI technologies into manufacturing processes is not only enhancing operational efficiency but also paving the way for a new era of smart factories where machines, systems, and human workers collaborate seamlessly.
Smart manufacturing, powered by AI, refers to the use of advanced algorithms, machine learning, robotics, and data analytics to optimize production processes, enhance quality control, and reduce downtime. Through the use of AI, production lines can be made more adaptive, predictive, and efficient, enabling manufacturers to stay competitive in a rapidly evolving global market.
This article will explore how AI is transforming the production line, providing examples of its successful implementation in various industries, and detailing the benefits and challenges associated with this shift. We will also dive into the technologies driving this change and explore the future of AI-driven manufacturing.
Section 1: Understanding Smart Manufacturing and AI Integration
To appreciate the impact of AI on manufacturing, it’s important to understand what smart manufacturing entails and how AI fits into the broader context of industrial automation.
What is Smart Manufacturing?
Smart manufacturing refers to the use of digital technologies to enhance manufacturing processes. It incorporates a range of technologies, such as AI, machine learning, IoT (Internet of Things), cloud computing, and robotics, to create highly adaptive and flexible production environments. These technologies work together to gather real-time data from sensors, machines, and production systems to optimize decision-making, streamline workflows, and improve overall productivity.
AI in Smart Manufacturing:
AI plays a critical role in smart manufacturing by providing systems with the ability to learn from historical data, predict outcomes, and make intelligent decisions. Machine learning algorithms are used to analyze data in real-time, enabling manufacturers to optimize operations, predict maintenance needs, and detect anomalies before they result in costly downtime. Additionally, AI is integral to robotics, automation systems, and digital twins, making manufacturing processes more efficient and reliable.
Key Technologies in AI-Powered Manufacturing
- Machine Learning (ML): Machine learning enables AI systems to learn from historical and real-time data to make better decisions. In manufacturing, ML algorithms can predict machine failures, optimize production schedules, and improve quality control.
- Robotics and Automation: AI-powered robots are capable of performing repetitive tasks with precision and efficiency. These robots can work alongside human workers or autonomously, handling complex manufacturing processes like assembly, inspection, and packaging.
- Computer Vision: Computer vision technologies enable AI systems to see and interpret the physical world. In manufacturing, this is used for quality inspection, defect detection, and automated assembly processes.
- Predictive Maintenance: AI systems equipped with predictive analytics can monitor machine health and detect potential failures before they occur. By analyzing sensor data from equipment, AI can predict when maintenance is needed, reducing downtime and improving the lifespan of machinery.
- Digital Twins: Digital twins are virtual replicas of physical machines, processes, or entire factories. AI-driven digital twins can simulate real-world manufacturing conditions and provide insights into how the physical systems are performing, allowing manufacturers to optimize processes and plan for potential disruptions.
Section 2: Case Studies of AI in Production Line Automation
AI has already proven its value in several industries, significantly enhancing the efficiency of production lines. In this section, we will look at real-world examples of AI applications in manufacturing that showcase the potential benefits of AI-driven automation.
Case Study 1: Siemens’ Smart Factory in Amberg, Germany
Siemens, a global leader in automation and industrial technology, has implemented one of the most advanced smart factories in the world at its Amberg facility in Germany. The factory, which produces automation equipment, has integrated AI technologies such as predictive analytics, robotics, and machine learning to optimize its production processes.
The AI system at the Amberg facility analyzes data from machines and sensors to optimize production schedules and ensure that production processes are running efficiently. Machine learning algorithms predict potential failures before they occur, allowing the facility to conduct proactive maintenance and avoid costly downtime.
One of the most impressive aspects of Siemens’ smart factory is its use of AI-powered robots. These robots work collaboratively with human employees, performing tasks such as assembly, inspection, and packaging. The use of AI ensures that the robots can adapt to changes in the production process and handle complex tasks with a high degree of precision.
Impact: Siemens’ smart factory has increased its production capacity by over 30% while maintaining high-quality standards. The integration of AI has reduced maintenance costs and downtime, leading to significant operational savings.
Case Study 2: General Electric’s Predictive Maintenance at Gas Turbine Plants
General Electric (GE), a global conglomerate that specializes in energy and industrial equipment, has been using AI-driven predictive maintenance technology in its gas turbine plants. By equipping turbines with IoT sensors, GE collects vast amounts of data on temperature, pressure, and vibration, which is then analyzed by AI systems to predict when maintenance will be needed.
The AI system uses machine learning to detect anomalies in the turbine’s operation and predict potential failures before they happen. This allows GE to perform maintenance on turbines only when necessary, rather than adhering to a fixed maintenance schedule. By avoiding unnecessary repairs and minimizing downtime, GE has been able to reduce maintenance costs and improve the efficiency of its turbine plants.
Impact: GE’s predictive maintenance technology has resulted in a 10-15% reduction in operational costs and improved the reliability of gas turbines, which are critical to power generation.
Case Study 3: Toyota’s AI-Driven Quality Control
Toyota, one of the world’s largest automakers, has adopted AI-driven quality control systems to enhance the efficiency of its production lines. The company uses computer vision and machine learning algorithms to inspect and detect defects in its vehicles during the assembly process.
By using AI to analyze images from cameras installed along the production line, Toyota can quickly identify defects such as paint imperfections, misaligned parts, or damaged components. The AI system is capable of detecting issues at a much faster rate than human inspectors, reducing the chances of defective products reaching the market.
Impact: Toyota’s AI-driven quality control system has improved production speed and accuracy, ensuring that the company can deliver high-quality vehicles to customers while reducing the need for costly manual inspections.
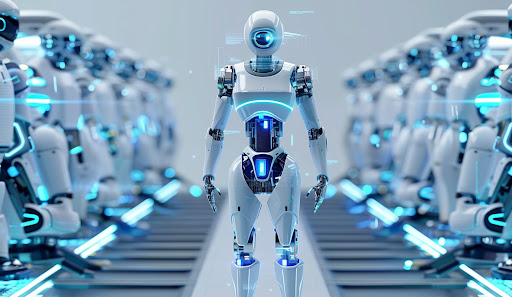
Section 3: Benefits of AI in Production Line Automation
The integration of AI into production lines offers numerous benefits, ranging from cost reduction to enhanced quality control. In this section, we will explore some of the key advantages that manufacturers experience when they incorporate AI into their operations.
1. Improved Efficiency and Productivity
AI-powered automation systems are capable of performing repetitive tasks more quickly and accurately than human workers. This leads to an increase in production speed and reduces cycle times. Additionally, AI can optimize production schedules, ensuring that manufacturing processes run smoothly and without delays.
2. Cost Reduction
By reducing downtime, improving maintenance schedules, and minimizing the need for manual labor, AI helps manufacturers significantly reduce operational costs. Predictive maintenance, for example, ensures that machines are only serviced when necessary, preventing unnecessary repairs and increasing equipment lifespan.
3. Enhanced Quality Control
AI-driven quality control systems provide higher precision and consistency in inspecting products, detecting defects, and ensuring that manufacturing standards are met. By utilizing computer vision and machine learning algorithms, AI can spot flaws that may be invisible to the human eye, ensuring that only high-quality products reach customers.
4. Greater Flexibility and Adaptability
AI enables manufacturing systems to adapt to changes in demand, production schedules, and market conditions. With AI, production lines can quickly switch between product types, adjust production rates, and respond to shifts in consumer preferences. This flexibility is essential in today’s fast-paced market, where consumer demands are constantly changing.
5. Data-Driven Decision Making
AI-driven manufacturing systems provide valuable data insights that help managers make informed decisions. By analyzing vast amounts of data collected from sensors, machines, and production systems, AI can uncover inefficiencies, predict trends, and provide actionable insights that improve overall production planning.
Section 4: Challenges and Considerations
While the integration of AI in manufacturing offers numerous benefits, it also comes with challenges. Manufacturers must carefully consider the following factors when implementing AI-driven automation on production lines:
1. High Initial Investment
Implementing AI in manufacturing requires significant upfront investment in both hardware and software. AI technologies such as machine learning, robotics, and computer vision require sophisticated infrastructure and specialized equipment, which can be expensive for smaller manufacturers.
2. Workforce Adaptation
The introduction of AI-powered automation may require changes in the workforce. While AI can reduce the need for manual labor in certain areas, it also creates new opportunities for skilled workers in fields such as data science, machine learning, and robotics. Manufacturers must invest in employee training and reskilling to ensure a smooth transition.
3. Data Privacy and Security
AI systems rely on vast amounts of data, much of which may be sensitive. Manufacturers must implement robust cybersecurity measures to protect against data breaches and ensure that AI systems are secure and compliant with data privacy regulations.
Section 5: The Future of AI in Smart Manufacturing
The future of smart manufacturing is promising, with AI playing a central role in driving further innovations. As AI technologies continue to evolve, we can expect even more advanced applications, such as fully autonomous production lines, collaborative robots (cobots) working alongside human workers, and even more personalized manufacturing processes.
Manufacturers will continue to leverage AI to enhance production efficiency, improve product quality, and stay ahead of the competition. With the rapid advancements in AI and automation, smart manufacturing will soon become the norm rather than the exception in industries worldwide.
Conclusion
AI-driven automation is fundamentally transforming the manufacturing landscape. From improved production efficiency and cost reduction to enhanced quality control and predictive maintenance, the integration of AI technologies on production lines is delivering significant advantages. Companies like Siemens, General Electric, and Toyota are already reaping the benefits of AI-powered smart manufacturing, showcasing how AI can revolutionize the manufacturing process.
As the industry continues to evolve, the future of manufacturing will be characterized by even greater levels of automation, efficiency, and customization. Manufacturers who embrace AI and automation will be better positioned to meet the demands of a fast-paced, global marketplace, driving innovation and staying competitive in the years to come.