Introduction
The manufacturing industry has long been a critical driver of economic growth and innovation. As technology advances, one of the most transformative forces reshaping the manufacturing sector is Artificial Intelligence (AI). AI is not only revolutionizing the way manufacturing processes are designed and optimized but is also enabling manufacturers to achieve new levels of efficiency, precision, and scalability.
From automating routine tasks to enhancing decision-making through predictive analytics, AI technologies are providing significant value in various aspects of manufacturing. These advancements allow companies to lower costs, reduce waste, improve product quality, and accelerate production cycles.
This article explores how AI is helping manufacturers increase production efficiency by delving into real-world case studies. We will explore key AI technologies such as machine learning, robotics, computer vision, and predictive maintenance, and demonstrate how they are being applied to solve manufacturing challenges and improve operations.
Section 1: AI Technologies Powering Manufacturing Efficiency
1.1 Machine Learning in Manufacturing
Machine learning (ML) algorithms are designed to learn from data, identify patterns, and make decisions based on past experiences. In manufacturing, machine learning is used to optimize production processes by analyzing historical data and predicting future outcomes.
- Predictive Maintenance: By analyzing data from sensors on machines and production lines, ML algorithms can predict when equipment is likely to fail, allowing for proactive maintenance. This helps reduce downtime and prevent costly repairs.
- Quality Control: Machine learning models can identify patterns in production data that are indicative of defects or quality issues. This can enable manufacturers to catch problems early in the production process and reduce waste.
Case Study: General Electric (GE)
General Electric uses machine learning to predict maintenance needs in its industrial equipment, such as turbines and engines. By analyzing sensor data in real-time, GE’s AI models can predict failures before they occur, minimizing downtime and keeping operations running smoothly.
1.2 Robotics and Automation
AI-powered robotics and automation systems are becoming integral to modern manufacturing. These robots can perform repetitive tasks with high precision, speed, and consistency, leading to improved production efficiency.
- Collaborative Robots (Cobots): Cobots work alongside human workers, assisting them with tasks such as assembly, material handling, and quality inspection. This collaboration between humans and machines increases throughput while ensuring worker safety.
- Automated Assembly Lines: Robots in automated assembly lines are capable of performing intricate tasks such as welding, packaging, and quality checks without human intervention, significantly speeding up the manufacturing process.
Case Study: Tesla
Tesla’s Gigafactories are known for their use of AI-driven robotics to streamline production. AI-powered robotic arms handle assembly tasks, increasing the speed and precision of production while reducing human error. Tesla’s innovative use of robots in production has enabled the company to scale production rapidly.
1.3 Computer Vision for Quality Inspection
AI-driven computer vision technologies can analyze images or video footage to detect defects or irregularities in products during the manufacturing process. These technologies use deep learning algorithms to improve their accuracy over time, ensuring consistent quality control.
- Automated Defect Detection: By using high-resolution cameras and AI-powered software, computer vision systems can scan products for defects and automatically sort or reject those that do not meet quality standards.
Case Study: BMW
BMW has implemented AI-powered computer vision in its manufacturing plants to perform quality checks on vehicle parts. The system can detect even the smallest defects in car body parts, which might go unnoticed by human inspectors. This reduces the risk of defective products reaching customers and enhances the overall quality of production.
1.4 Predictive Analytics for Supply Chain Optimization
AI-based predictive analytics helps manufacturers optimize their supply chains by analyzing historical data, market trends, and customer demand. These insights allow for better decision-making related to inventory management, production planning, and procurement.
- Demand Forecasting: By predicting demand patterns, AI can help manufacturers produce the right amount of inventory, reducing excess stock or shortages.
- Supply Chain Risk Management: AI can also be used to predict potential disruptions in the supply chain, such as raw material shortages or transportation delays, allowing manufacturers to adjust production schedules accordingly.
Case Study: Siemens
Siemens uses AI and predictive analytics to optimize its global supply chain. The company leverages machine learning models to analyze various data sources, allowing it to forecast demand and manage inventory efficiently. This approach has helped Siemens reduce supply chain costs and improve delivery times.
Section 2: Real-World Examples of AI in Manufacturing
2.1 Case Study: Intel’s Smart Factory Initiatives
Intel has made significant strides in implementing AI to improve its manufacturing processes. The company uses AI to monitor and optimize the performance of its semiconductor production lines. By analyzing data from sensors and production systems, Intel’s AI tools help detect inefficiencies and optimize operations. The company has reported significant improvements in yield rates and cost reductions as a result of these AI-driven innovations.
2.2 Case Study: Rolls-Royce’s AI in Aircraft Engine Manufacturing
Rolls-Royce has implemented AI to enhance its manufacturing processes, particularly in the production of aircraft engines. AI models are used to predict maintenance needs for engines in the field and monitor the performance of the engines during production. By integrating AI into both production and maintenance, Rolls-Royce is able to provide more reliable and efficient engine manufacturing services.
2.3 Case Study: Ford’s AI-Powered Production Lines
Ford has introduced AI-powered robots and automation technologies into its production lines to enhance operational efficiency. AI is used to optimize workflows and adjust production schedules in real-time based on demand fluctuations and operational requirements. By incorporating AI into its manufacturing processes, Ford has been able to increase production speed, reduce defects, and improve overall efficiency.
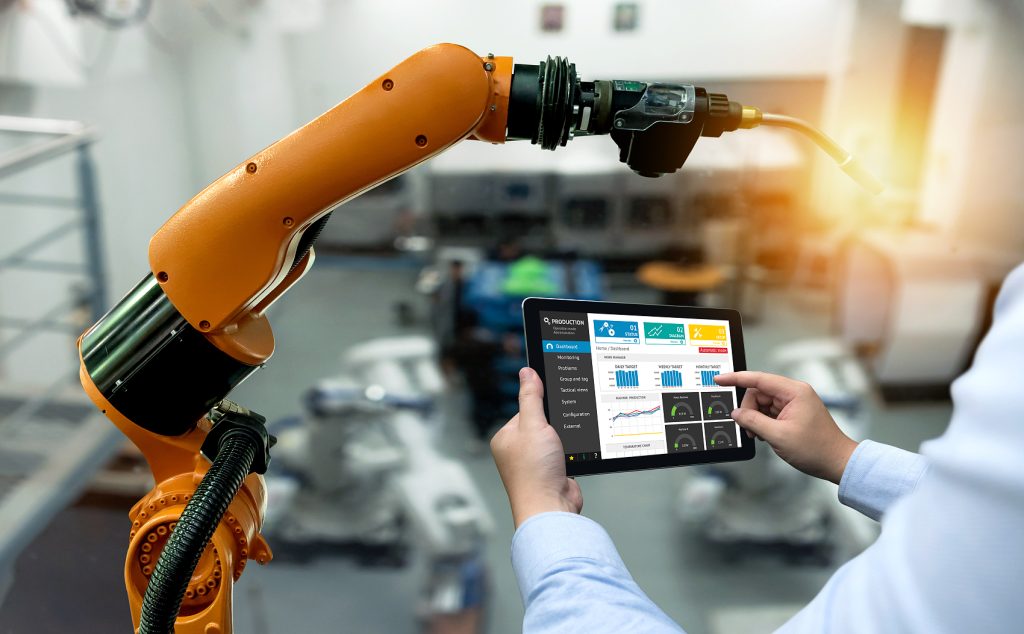
Section 3: How AI is Transforming Specific Aspects of Manufacturing
3.1 Energy Efficiency
AI technologies can optimize energy usage in manufacturing plants by analyzing consumption patterns and adjusting operations to minimize energy waste. Machine learning algorithms can predict periods of high energy demand and suggest ways to adjust production schedules or equipment usage to reduce energy costs.
3.2 Human-Robot Collaboration
AI enables more seamless collaboration between human workers and robots on the factory floor. Cobots, which are robots designed to work alongside humans, can assist with tasks that require precision, strength, or repetition. This collaboration boosts efficiency by allowing humans to focus on tasks that require creativity, decision-making, or flexibility, while robots handle repetitive or physically demanding jobs.
3.3 Real-Time Monitoring and Feedback Loops
AI enables continuous monitoring of production processes and provides real-time feedback to operators. AI systems can detect any deviations from the standard process and alert operators to potential issues. This real-time feedback loop ensures that any problems are addressed immediately, minimizing disruptions and maintaining production efficiency.
Section 4: Challenges in Implementing AI in Manufacturing
4.1 High Initial Investment
The implementation of AI technologies in manufacturing can require significant initial investment in terms of both hardware and software. Many manufacturers may struggle to justify the high costs associated with AI adoption, particularly small and medium-sized enterprises (SMEs).
4.2 Data Quality and Integration
AI systems rely heavily on data to make informed decisions. One of the key challenges in implementing AI is ensuring that data is accurate, clean, and integrated across various platforms and systems. Manufacturers must invest in data collection infrastructure and processes to ensure that AI tools have access to the right information.
4.3 Workforce Reskilling
The introduction of AI into manufacturing environments often requires workers to acquire new skills, particularly in programming, robotics, and data analysis. Companies need to invest in training and reskilling programs to ensure that their workforce is prepared for the changes AI brings.
Section 5: The Future of AI in Manufacturing
5.1 The Evolution of AI Technologies
AI technologies are evolving rapidly, with new innovations in machine learning, robotics, and data analytics continuously improving manufacturing processes. As AI becomes more advanced, it will be able to automate even more complex tasks and provide deeper insights into production efficiency.
5.2 Industry 4.0 and Smart Factories
AI is at the core of the Industry 4.0 revolution, which is transforming manufacturing into a more interconnected, automated, and intelligent sector. Smart factories, where machines, robots, and humans work together in an AI-powered ecosystem, are the future of manufacturing. These factories will be able to optimize production in real-time, adapt to changing conditions, and improve efficiency at an unprecedented scale.
5.3 The Role of AI in Sustainable Manufacturing
As manufacturers face increasing pressure to reduce their environmental impact, AI can play a critical role in achieving sustainability goals. AI can optimize energy usage, reduce waste, and improve resource management, helping companies minimize their carbon footprints and contribute to more sustainable manufacturing practices.
Conclusion
AI is transforming the manufacturing industry by improving production efficiency, enhancing quality control, and streamlining operations. From predictive maintenance and robotics to machine learning and computer vision, AI technologies are enabling manufacturers to reduce costs, increase output, and deliver higher-quality products.
However, implementing AI in manufacturing comes with its own set of challenges, including high initial investment costs, data integration issues, and the need for workforce reskilling. Despite these obstacles, the potential benefits of AI in manufacturing are immense, and as technology continues to evolve, the future of AI-driven manufacturing looks bright.
By embracing AI, manufacturers can unlock new levels of productivity, efficiency, and sustainability, positioning themselves for success in the increasingly competitive global market.